Galvanized pipes play a crucial role in various industries and infrastructure due to their inherent resistance to corrosion and rust. The process of coating iron or steel with zinc through galvanization creates a protective barrier against moisture, oxygen, and ultraviolet light, all of which are common causes of metal degradation. This preservation of structural integrity is vital for pipes exposed to harsh environmental conditions or carrying fluids prone to causing corrosion.
Whether through hot-dip galvanizing or pre-galvanizing methods, the application of zinc ensures the prolonged durability and reliability of the pipes. This safeguarding extends the lifespan of infrastructure, reduces maintenance costs, and enhances operational efficiency. In essence, galvanized pipes serve as guardians of the flow, safeguarding the integrity of pipelines and ensuring uninterrupted transportation of fluids. Understanding the essentials of galvanized pipes is paramount for maintaining infrastructure resilience and sustaining essential services across various sectors.
Understanding Galvanized Pipes
Definition and Composition of Galvanized Pipes
Galvanized pipes are crafted from iron or steel and coated with a protective layer of zinc to thwart corrosion and rust. This protective measure is achieved through the process of galvanization, which can occur via hot-dip galvanizing or pre-galvanizing methods. In hot-dip galvanizing, pipes are submerged in a molten zinc bath, while pre-galvanizing involves coating steel coils with zinc before shaping them into pipes. This zinc coating forms a robust barrier that shields the underlying metal from environmental elements, ensuring prolonged durability and resilience against corrosion.
Advantages
- Corrosion Resistance: Galvanized pipes exhibit exceptional resistance to corrosion, thereby extending their lifespan.
- Durability: The zinc coating enhances the pipes' strength and resilience, rendering them suitable for diverse applications.
- Cost-Effectiveness: Galvanized pipes necessitate minimal maintenance and boast a comparatively low initial cost.
- Versatility: Galvanized pipes find utility in both indoor and outdoor settings, catering to a broad spectrum of applications.
Disadvantages
- Limited Lifespan: Despite their corrosion resistance, galvanized pipes may degrade over time, especially in corrosive environments.
- Vulnerability to Mechanical Damage: The zinc coating is susceptible to damage from scratches or dents, compromising its protective qualities.
- Potential for Zinc Leaching: Under specific conditions, such as acidic environments, the zinc coating may degrade, resulting in zinc leaching into water systems.
Common Applications
- Plumbing Systems: Galvanized pipes are prevalent in residential, commercial, and industrial plumbing systems for fluid transport.
- Gas Distribution: Their corrosion resistance and durability make galvanized pipes suitable for gas distribution lines.
- Construction and Infrastructure: Galvanized pipes serve in construction projects like scaffolding, handrails, fencing, and structural support for buildings and bridges.
- Agricultural Applications: Galvanized pipes are utilized in agricultural irrigation systems, fencing, and livestock enclosures, enduring harsh outdoor conditions and resisting corrosion effectively.
Shenlong's Hot Dip Galvanized Steel Pipe Specification
Shenlong, renowned for its commitment to quality, offers a comprehensive specification for hot dip galvanized steel pipes, ensuring reliability and longevity in various applications.
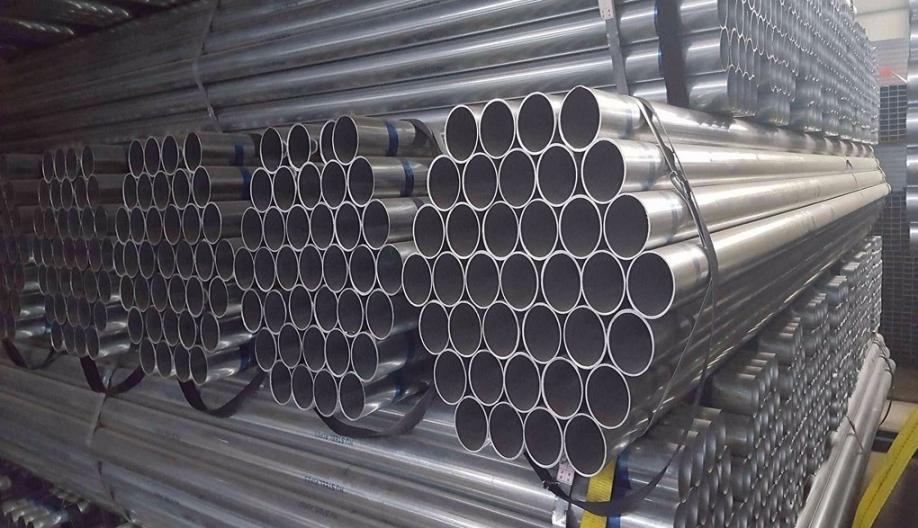
Standard Compliance
Conforming to international standards such as GB/T3091-2001, A53, EN10255, DIN2440, BS1387, among others, Shenlong's hot dip galvanized steel pipes guarantee adherence to rigorous quality benchmarks.
Materials Used
Shenlong employs high-grade materials including Q235, Q345B, Gr.B, S195T, ST35, ensuring robustness and durability in every pipe manufactured.
Dimensions and Specifications
- Outer Diameter: Ranging from 1/4" to 40", Shenlong's pipes accommodate various project requirements with precision.
- Wall Thickness: Extending from Sch5 to Sch80 (1.0mm – 4mm), Shenlong offers flexibility to cater to diverse industrial needs.
- Length: Available in lengths spanning from 2m to 12m, these pipes facilitate efficient installation and deployment across projects of varying scales.
Applications
Shenlong's hot dip galvanized steel pipes find extensive utility across a spectrum of industries, including construction, fire control, and pipeline infrastructure. Their versatility makes them indispensable for structural support, fluid transport, and containment systems, among other applications.
Hot Dip Galvanized Steel Pipe Advantages
- Compliance with ISO Standards: Shenlong's hot dip galvanized steel pipes adhere to ISO standards for zinc layer thickness, ensuring consistent and reliable performance in diverse environments.
- Superior Corrosion Resistance: The zinc coating on Shenlong's pipes offers exceptional protection against corrosion, safeguarding the structural integrity and longevity of the infrastructure. This corrosion resistance is crucial for applications exposed to harsh environmental conditions and corrosive elements.
- Quality Assurance: Shenlong's commitment to quality extends to every stage of production, from material selection to manufacturing processes. This dedication ensures that each hot dip galvanized steel pipe meets stringent quality standards and exceeds customer expectations.
Repairing Galvanized Pipes
Identifying Leaks and Damages
- Regular inspections are essential for identifying galvanized pipes' leaks, corrosion spots, and damages.
- Look for signs such as rust spots, discoloration, or moisture around joints and connections.
- Utilize tools like pressure tests or leak detection kits to pinpoint hidden leaks or weaknesses in the pipe structure.
Temporary Fixes for Minor Issues
- In case of minor leaks or surface damages, temporary fixes can prevent further deterioration.
- Use epoxy putty or rubber patches to seal small leaks temporarily.
- Wrapping damaged areas with waterproof tape or silicone can provide a short-term solution until permanent repairs can be made.
Permanent Repair Methods
- Patching and Sealing Techniques:
Clean the damaged area thoroughly and remove any rust or debris. Apply a galvanized metal primer to promote adhesion of the patching material. Use epoxy-based compounds or galvanized repair clamps to seal leaks and reinforce weakened areas.
- Pipe Replacement Options:
If the damage is extensive or the pipe is nearing the end of its lifespan, consider replacing sections or the entire length of the galvanized pipe. Choose replacement pipes made from durable materials like stainless steel or PVC to ensure long-term reliability.
Preventative Measures
Strategies for Preventing Corrosion
- Regularly inspect and maintain galvanized pipes to identify and address corrosion early.
- Implement cathodic protection systems or sacrificial anodes to prevent galvanic corrosion.
- Control environmental factors such as moisture and humidity to minimize corrosion risk.
Implementing Protective Coatings
- Apply corrosion-resistant coatings or paints to galvanized pipes to provide an additional layer of protection.
- Consider using epoxy or polyurethane coatings for enhanced durability and resistance to abrasion.
- Ensure proper surface preparation and application techniques for effective coating adhesion.
Environmental Considerations
- Minimize exposure of galvanized pipes to harsh chemicals or corrosive substances.
- Implement proper drainage systems to prevent standing water or moisture accumulation around pipe installations.
- Consider environmental factors such as soil composition and pH levels when designing pipe installations to mitigate corrosion risks.
Safety Guidelines
Handling and Working with Galvanized Pipes Safely:
Wear appropriate personal protective equipment (PPE) such as gloves and safety goggles when handling galvanized pipes. Use caution when cutting or welding galvanized pipes to avoid inhalation of zinc fumes, which can cause respiratory irritation. Follow proper lifting and handling techniques to prevent injuries when moving heavy pipes or equipment.
Risks Associated with Galvanized Pipes and How to Mitigate Them
Be aware of potential hazards such as corrosion, leaks, and structural weaknesses associated with galvanized pipes. Regularly inspect pipes for signs of deterioration and address any issues promptly to prevent accidents or failures. Educate personnel on proper maintenance practices and emergency procedures to mitigate risks associated with galvanized pipes.
Proper Disposal Practices for Old or Damaged Pipes
Dispose of old or damaged galvanized pipes in accordance with local regulations and environmental guidelines. Consider recycling options for metal pipes to minimize waste and reduce environmental impact. Consult with waste management professionals or recycling facilities for proper disposal methods and procedures.
CONCLUSION
mastering the essentials of galvanized pipes is paramount for safeguarding infrastructure and ensuring uninterrupted fluid transportation. From understanding their composition to implementing preventative measures, galvanized pipe essentials serve as the guardians of the flow, protecting against corrosion, leaks, and structural weaknesses. By adhering to safety guidelines and employing proper repair and maintenance techniques, we can prolong the lifespan of galvanized pipes and uphold the integrity of our plumbing systems, construction projects, and industrial infrastructure. Embracing these essentials not only enhances reliability and durability but also contributes to sustainable and resilient infrastructure development.